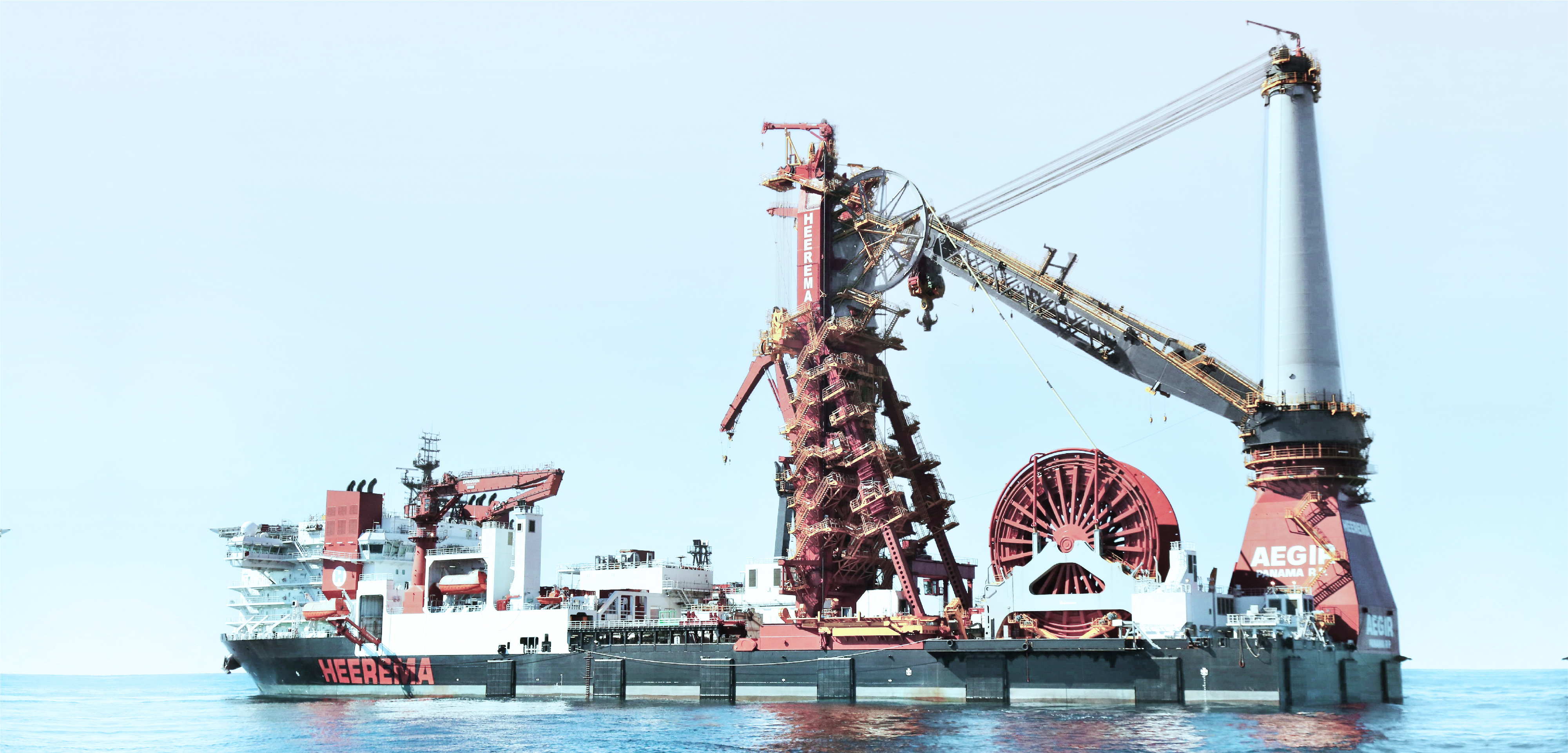
Load Moment Control
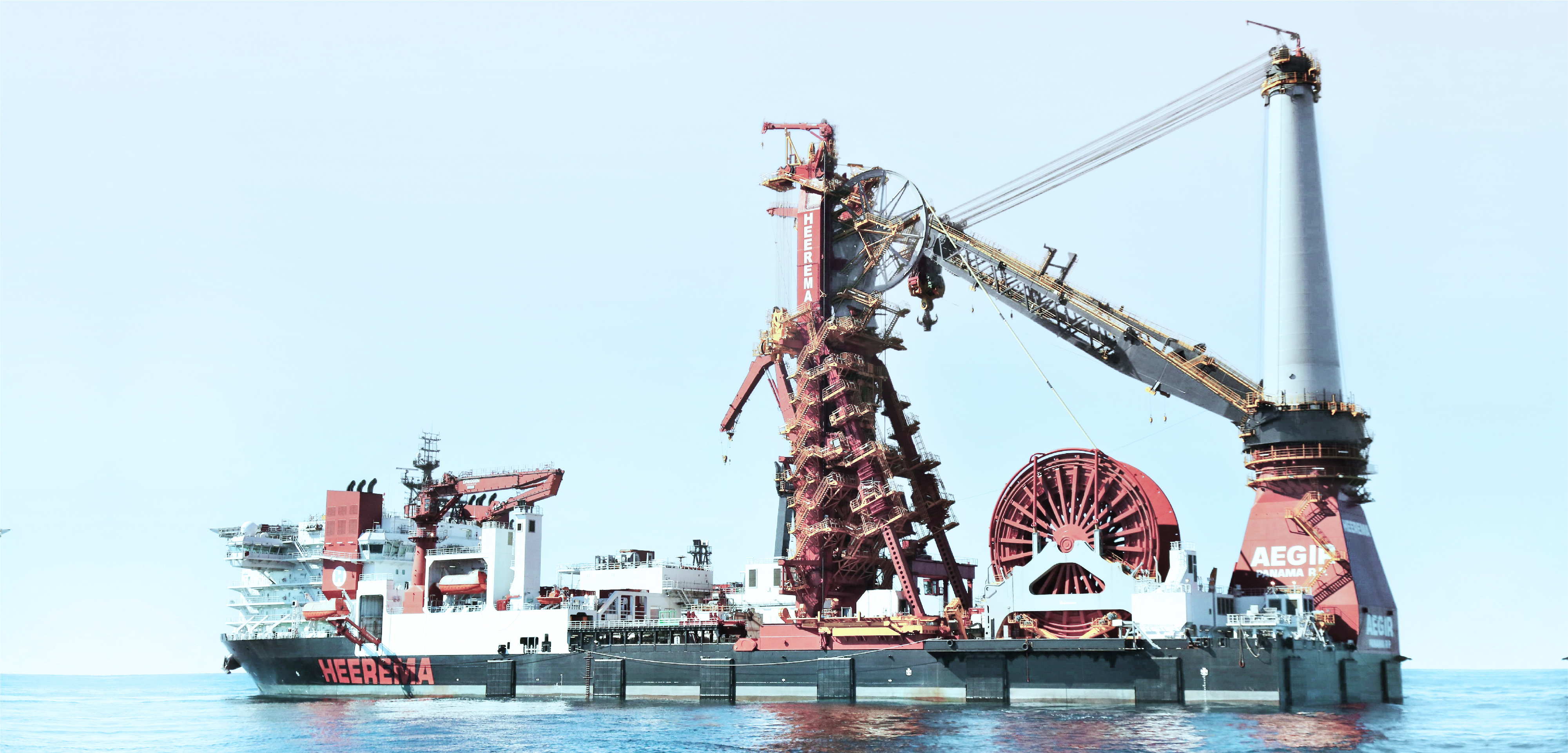

System Overview
- Description
The Load Moment Control (LMC) algorithm considers the impact of the crane slewing process under a given load on the vessel’s floating condition. LMC computes the exact magnitude of counter-acting moment to keep the crane vessel in the defined floating condition within a narrow window of tolerance. In principle, the “ballast follows the crane” by automatically shifting the required amount of ballast water in-between heeling tanks to compensate the crane’s righting moment. This is achieved by controlling the individual flow, in a four-quadrant operation, in each heeling tank pair with frequency controlled reversible propeller pumps. The LMC mode includes general pump, turbine and zero flow operation of the pump. The novel control algorithm was developed for Heerema’s Aegir, a 210 m deepwater construction vessel for heavy lift and pipe laying installations. The vessel is equipped with a 4,000 t offshore crane with a radius of up to 40 m, located stern offset to starboard. Locating the crane off centre line to starboard introduced a significantly high overturning moment on the vessel that required a sophisticated Heel Control system to ensure a safe and economically feasible operation. The application of LMC fulfilled these demands and ensured to keep the Aegir upright in all operational conditions with +/- 0.5 degrees heel.