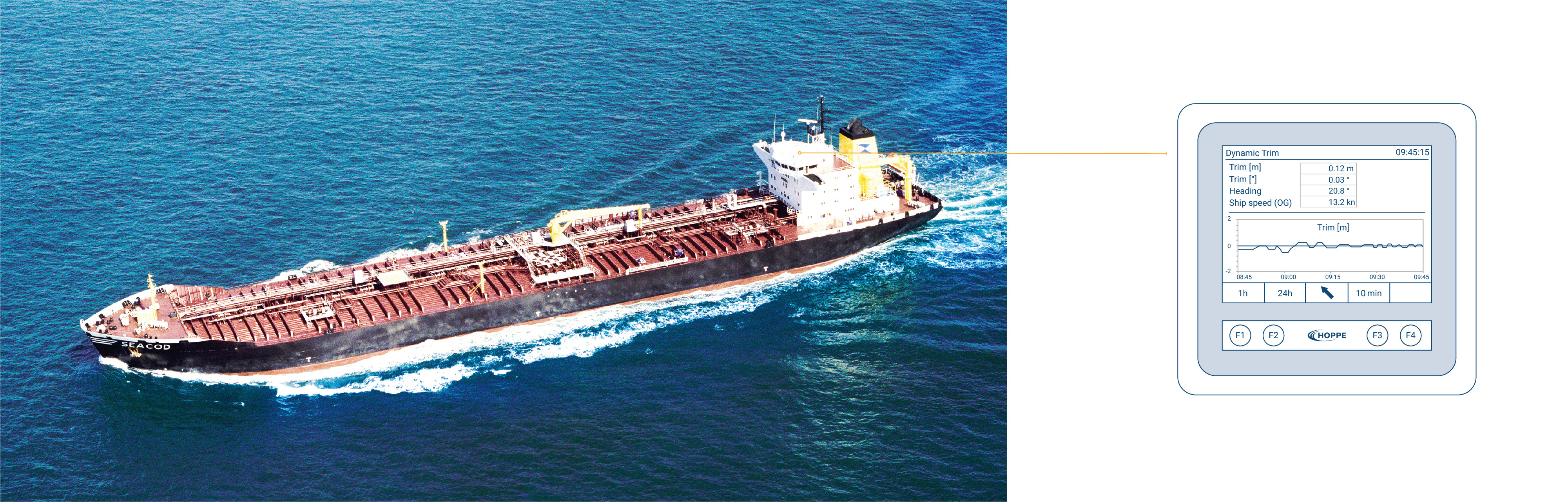
Dynamic Draught, Trim and Motion Measurement
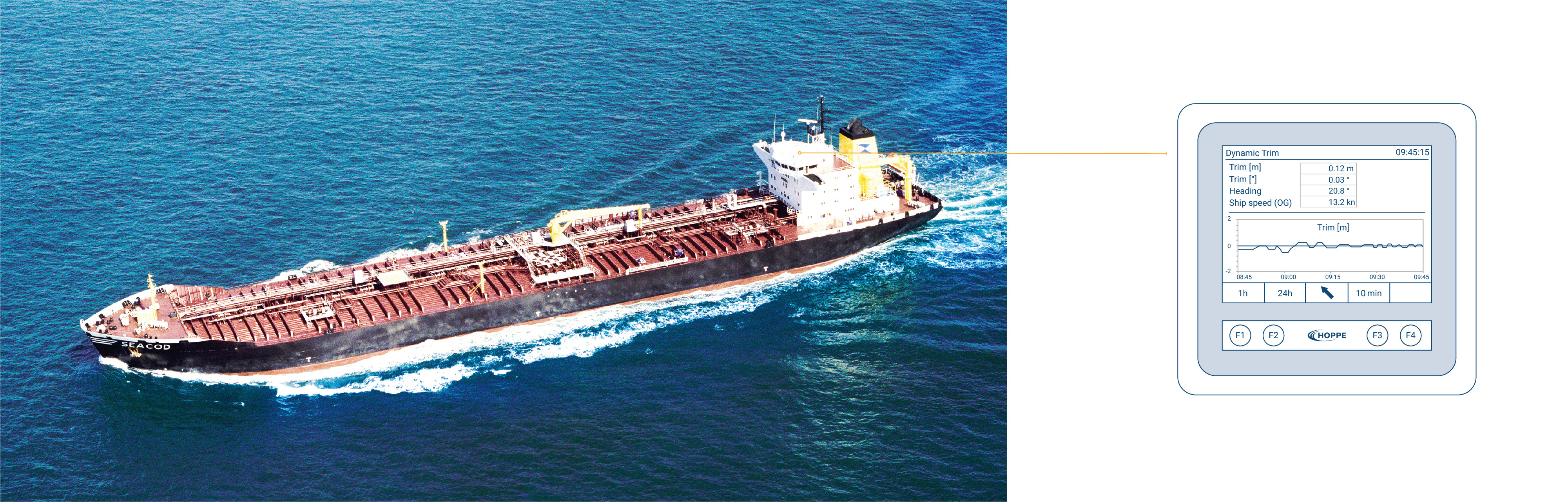
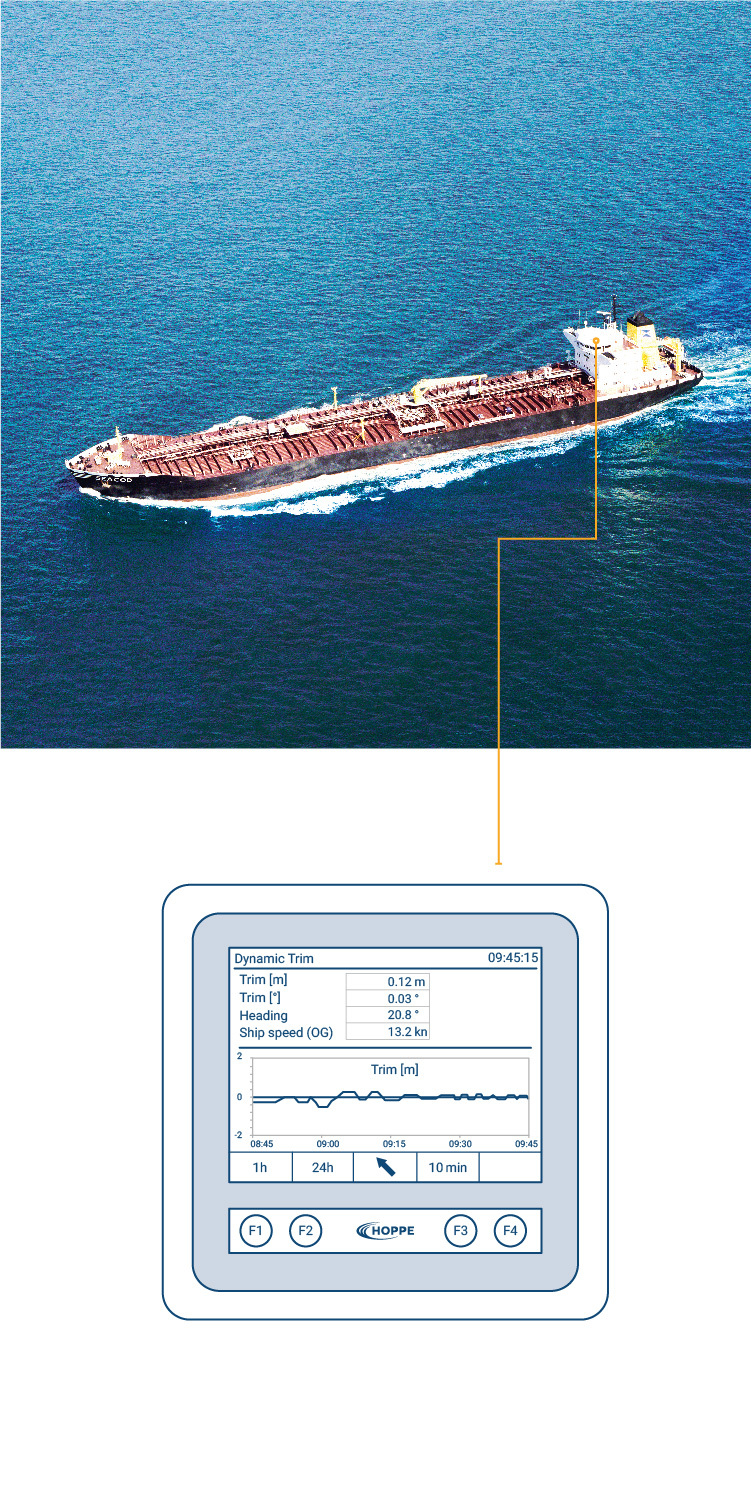
System Overview
- Description
- Key Features
Our Dynamic Draught Measurement Solution (DDM) continuously monitors the ship‘s draught by combining draught and motion sensors. Pressure transmitters measure the hydrostatic draught, one each located at bow, stern, mid ship port and mid ship starboard. With our inertial measuring system (HOSIM2) we compensate any dynamic influence during sailing. This makes the draught measuring system independent of wave effects or wave hammering. It determines the draught values precisely at perpendiculars and draught marks in any sailing condition.
HOPPE Marine‘s Dynamic Trim Measurement (TRIMCON) is a satellite-based measuring system for real time monitoring of a ship’s dynamic trim, heading and speed in longitudinal and athwart directions. Two GPS-receivers located on the fore and aft mast are using carrier phase measurements. The significant advantage of TRIMCON is the continuous and precise determination of the dynamic trim in almost every sailing condition.
The system assists the Nautical Officers with precise information on actual pitch angle and dynamic trim and monitors the ship‘s fore and aft relative motion with high precision during manoeuvring. The dynamic trim varies under sea conditions with the ship’s speed, bottom clearance and tank contents and needs to be corrected for a fuel-optimised ship operation.
HOPPE Marine Dynamic Motion Measurement is an inertial measuring system with two sensor boxes (HOSIM2), one at the bow and one at the stern, that continuously monitor the ship’s motion and hull stress. It is the highly accurate solution for the roll angle, pitch angle, angular rate, angular acceleration, orbital acceleration, roll and pitch period, ship‘s torsion, as well as trim and list. The provided information can be used by subsequent systems or by nautical staff to better evaluate questions regarding cargo safety, ship performance and general ship safety.
Dynamic Draught Measurement
- Precise determination of real draughts
- Basis of trim optimization
- Possibility of draught, trim and speed modeling
Dynamic Trim Measurement
- True dynamic trim
- Conning information
- Shallow water pilotage
Dynamic Motion Measurement
- Precise vessel motions
- Rolling, pitch and acceleration forces
- Hogging and sagging
- Sea state modeling
Components
- Overview
Dynamic Draught Measurement
- 4 draught sensors (optionally only 2)
- 2 HOSIM2 IMU Sensors1
- HOMIP PLC unit
Dynamic Trim Measurement
- 2 GPS antennas with signal amplifiers2
- HOMIP PLC unit
Dynamic Motion Measurement
- 2 HOSIM2 IMU sensors
- HOMIP PLC unit
1 alternatively 2 GPS sensors 2 alternatively 2 IMU sensors
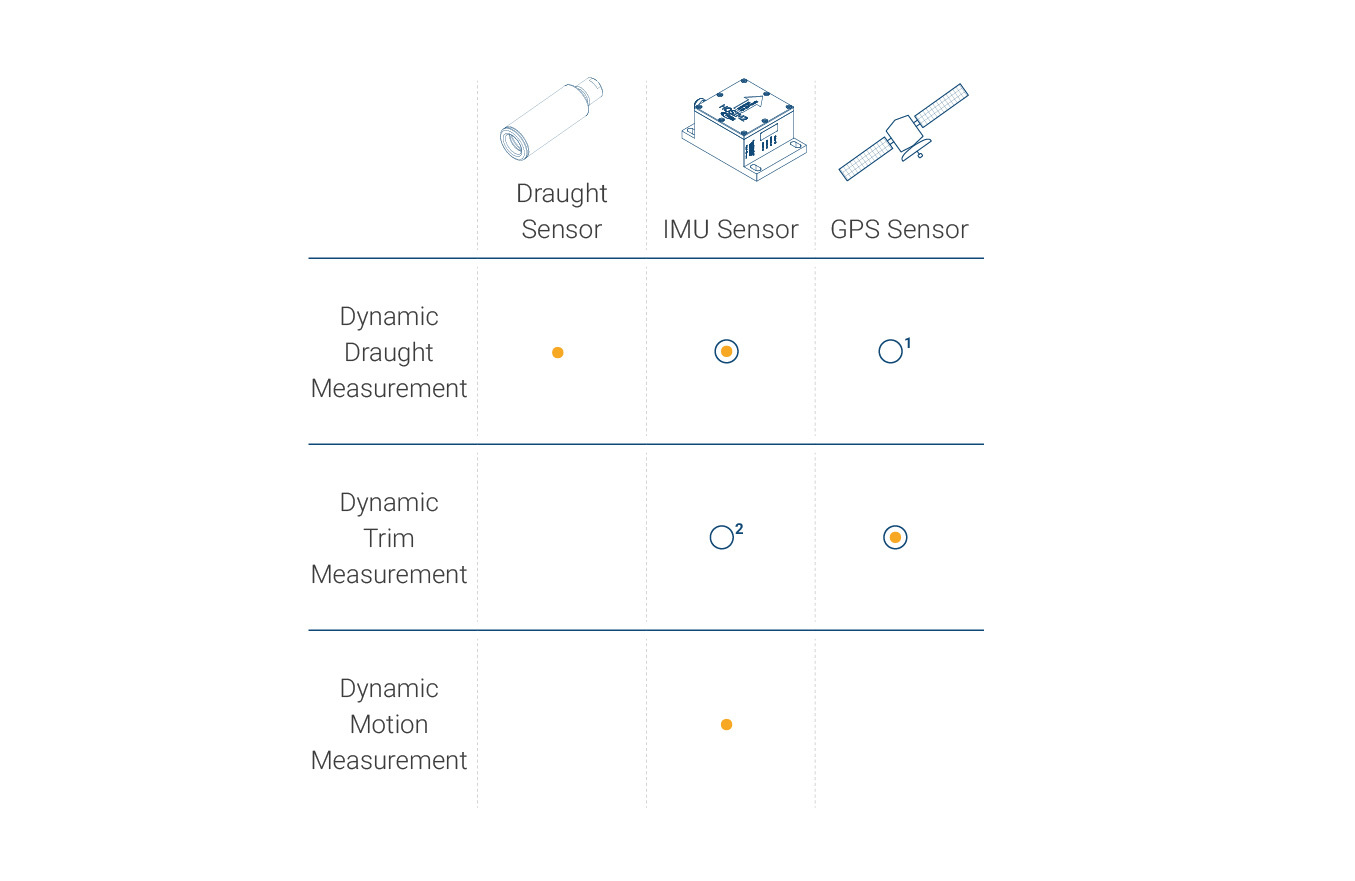